Active Current Compensation (ACC) refers to a technique used in power electronics to mitigate or eliminate undesirable current harmonics or distortions in electrical systems. The trigger mechanism initiates the compensating action to mitigate these unwanted harmonics and maintain the quality of the electrical power. The following will briefly introduce the existing ACC technology and the factors of trigger ACC.
Technology of Active Current Compensation
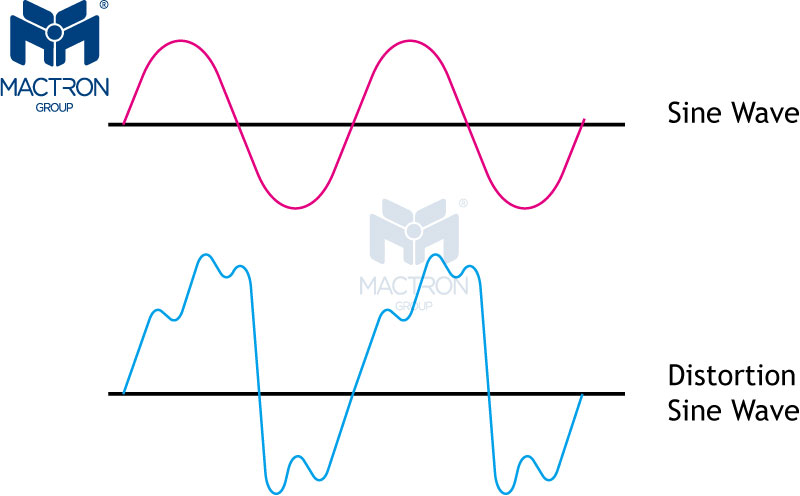
The primary objective of ACC is to maintain the sinusoidal shape of the current waveform and ensure that it closely follows the fundamental frequency of the electrical system. By doing so, ACC helps to improve power quality, reduce losses, and prevent adverse effects such as voltage distortion, overheating of equipment, and interference with other electrical devices.
There are several methods and devices used to implement ACC, including:
There are several methods and devices used to implement ACC, including:
Active Harmonic Filters (AHFs):
These are electronic devices that actively inject compensating currents into the electrical system to cancel out harmonic currents generated by nonlinear loads. AHFs typically use power electronics converters, such as voltage-source inverters, to generate the compensating currents.
Active Power Filters (APFs):
Similar to AHFs, APFs are devices that inject compensating currents into the system to mitigate harmonic distortions. In addition to compensating for harmonic currents, APFs can also provide reactive power compensation and voltage regulation.
Active Front-End Converters:
In some applications, such as variable frequency drives (VFDs) and uninterruptible power supplies (UPS), active front-end converters are used to control the input current waveform to the system. These converters actively shape the current waveform to reduce harmonic content and improve power factor.
Digital Signal Processing (DSP) Control:
ACC systems often employ digital signal processing techniques to analyze the current waveform and generate compensating signals in real-time. DSP-based control algorithms can adapt to changing system conditions and effectively compensate for harmonic currents over a wide range of operating conditions.
These are electronic devices that actively inject compensating currents into the electrical system to cancel out harmonic currents generated by nonlinear loads. AHFs typically use power electronics converters, such as voltage-source inverters, to generate the compensating currents.
Active Power Filters (APFs):
Similar to AHFs, APFs are devices that inject compensating currents into the system to mitigate harmonic distortions. In addition to compensating for harmonic currents, APFs can also provide reactive power compensation and voltage regulation.
Active Front-End Converters:
In some applications, such as variable frequency drives (VFDs) and uninterruptible power supplies (UPS), active front-end converters are used to control the input current waveform to the system. These converters actively shape the current waveform to reduce harmonic content and improve power factor.
Digital Signal Processing (DSP) Control:
ACC systems often employ digital signal processing techniques to analyze the current waveform and generate compensating signals in real-time. DSP-based control algorithms can adapt to changing system conditions and effectively compensate for harmonic currents over a wide range of operating conditions.
Trigger of Active Current Compensation

ACC plays a critical role in modern power systems. By actively compensating for harmonic currents, ACC helps to maintain power quality and ensure the stable operation of electrical systems.
The trigger for ACC can be based on various factors, including:
Current Monitoring:
ACC systems continuously monitor the current waveform using sensors or measurement devices. When the current waveform deviates from the desired sinusoidal shape or exceeds predefined harmonic distortion limits, the ACC system is triggered to take corrective action.
Voltage Monitoring:
In some cases, ACC systems may trigger based on voltage measurements, especially if voltage distortions are correlated with current distortions. Voltage monitoring helps detect system-wide disturbances that may affect power quality and trigger compensating action accordingly.
Predefined Thresholds:
ACC systems often have predefined thresholds for harmonic distortion levels or power quality indices. When the measured values exceed these thresholds, the ACC system is triggered to activate compensating devices or algorithms to mitigate the disturbances.
Control Signals:
In systems with centralized control, such as active harmonic filters (AHFs) or active power filters (APFs), the trigger may be initiated by control signals from a central controller or supervisory system. These control signals are based on real-time analysis of system conditions and trigger compensating action as needed.
User Commands:
In some applications, users may have the ability to manually trigger ACC operation based on their specific requirements or preferences. For example, users may activate ACC to mitigate harmonic distortions during critical operations or when sensitive equipment is in use.
Current Monitoring:
ACC systems continuously monitor the current waveform using sensors or measurement devices. When the current waveform deviates from the desired sinusoidal shape or exceeds predefined harmonic distortion limits, the ACC system is triggered to take corrective action.
Voltage Monitoring:
In some cases, ACC systems may trigger based on voltage measurements, especially if voltage distortions are correlated with current distortions. Voltage monitoring helps detect system-wide disturbances that may affect power quality and trigger compensating action accordingly.
Predefined Thresholds:
ACC systems often have predefined thresholds for harmonic distortion levels or power quality indices. When the measured values exceed these thresholds, the ACC system is triggered to activate compensating devices or algorithms to mitigate the disturbances.
Control Signals:
In systems with centralized control, such as active harmonic filters (AHFs) or active power filters (APFs), the trigger may be initiated by control signals from a central controller or supervisory system. These control signals are based on real-time analysis of system conditions and trigger compensating action as needed.
User Commands:
In some applications, users may have the ability to manually trigger ACC operation based on their specific requirements or preferences. For example, users may activate ACC to mitigate harmonic distortions during critical operations or when sensitive equipment is in use.
Benefits of Applying Active Current Compensation in Industrial PC Field

Applying ACC in the industrial PC field offers several benefits:
Improved Power Quality:
ACC can monitor and compensate for harmonic distortions and voltage fluctuations in the electrical grid, enhancing the power quality of industrial PC systems. A stable power supply helps reduce equipment failures and enhances system reliability.
Equipment Protection:
ACC reduces the risk of equipment damage and failures caused by harmonics and voltage fluctuations. By promptly compensating for current distortions in the grid, ACC protects industrial PCs and related equipment, prolonging their lifespan.
Enhanced Energy Efficiency:
ACC optimizes the power factor of industrial PC systems and reduces energy losses resulting from harmonic currents and voltage fluctuations. Improved energy utilization helps lower energy costs and boost system efficiency.
Reduced Downtime:
A stable power supply minimizes production downtime due to equipment failures and power quality issues. ACC ensures the reliable operation of industrial PC systems, reducing the risk of production interruptions.
Increased Productivity:
Stable power supply and equipment protection improve productivity. The continuous and reliable operation of industrial PC systems ensures production continuity and reliability, leading to increased productivity.
Lower Maintenance Costs:
By reducing equipment failures and extending equipment lifespan, ACC lowers maintenance costs. A stable power supply helps reduce equipment maintenance and repair frequency, lowering maintenance expenses.
In summary, implementing ACC in the industrial PC domain improves power quality, protects equipment, enhances energy efficiency, reduces downtime, increases productivity, and lowers maintenance costs. This ensures stable and reliable power support for industrial production, ultimately enhancing overall production efficiency.
Improved Power Quality:
ACC can monitor and compensate for harmonic distortions and voltage fluctuations in the electrical grid, enhancing the power quality of industrial PC systems. A stable power supply helps reduce equipment failures and enhances system reliability.
Equipment Protection:
ACC reduces the risk of equipment damage and failures caused by harmonics and voltage fluctuations. By promptly compensating for current distortions in the grid, ACC protects industrial PCs and related equipment, prolonging their lifespan.
Enhanced Energy Efficiency:
ACC optimizes the power factor of industrial PC systems and reduces energy losses resulting from harmonic currents and voltage fluctuations. Improved energy utilization helps lower energy costs and boost system efficiency.
Reduced Downtime:
A stable power supply minimizes production downtime due to equipment failures and power quality issues. ACC ensures the reliable operation of industrial PC systems, reducing the risk of production interruptions.
Increased Productivity:
Stable power supply and equipment protection improve productivity. The continuous and reliable operation of industrial PC systems ensures production continuity and reliability, leading to increased productivity.
Lower Maintenance Costs:
By reducing equipment failures and extending equipment lifespan, ACC lowers maintenance costs. A stable power supply helps reduce equipment maintenance and repair frequency, lowering maintenance expenses.
In summary, implementing ACC in the industrial PC domain improves power quality, protects equipment, enhances energy efficiency, reduces downtime, increases productivity, and lowers maintenance costs. This ensures stable and reliable power support for industrial production, ultimately enhancing overall production efficiency.
Take a look at the MAV series of MACTRON GROUP(MTG).
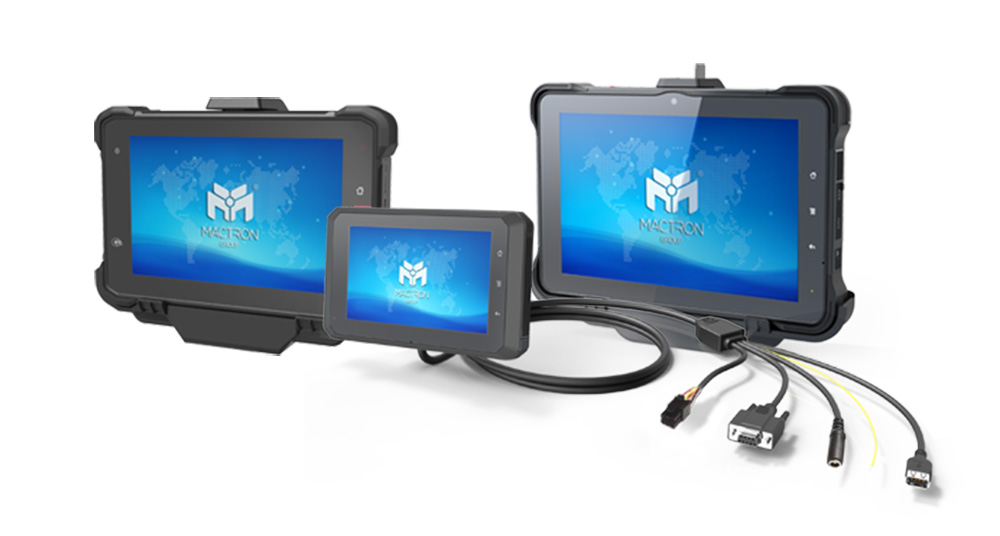
Our MAV series products are all equipped with ACC input, which can support you to detect and respond to harmonic distortions, and contribute to improved system performance, energy efficiency, and overall reliability. Contact us for more information on which MAV product is adequate for you.
0 comments:
Post a Comment